Specification
The new development direction of distribution transformers
Source:Original
Editing:frank
Time:2022-02-22 17:55
With the development of electrical material production, the mechanical manufacturing department supplying the production process equipment of distribution transformer has developed rapidly, and a large number of new knowledge in the field of mechanization and automation of production process have emerged. All these make the production of transformer appear some new directions.
In recent years, the biggest change in the production of distribution transformer coil is the use of aluminum enameled wire, and the transition to winding with thin aluminum belt. The cooling system of oil immersed distribution transformer has also been improved. The air tightness of oil tank is a development trend, and there are also significant changes in the production process of transformer core.
It can be said that the historic changes in the distribution transformer dance represented by the production of enamelled aluminum wire, antioxidant transformer oil and cast insulated transformer are as significant as the use of directional silicon steel strip during the postwar period.
At present, the high-voltage winding of distribution oil immersed transformer is characterized by the use of enameled aluminum wire and aluminum strip. When the cross-section of the wire is not large, the paint can not be used only when the cross-section of the wire is not large. Fundamental changes have also taken place in the low-voltage winding. At present, the unified winding made of thin aluminum strip and interlayer insulation winding is gradually replacing various types and models of windings for transformers with a capacity of 100 to 1600 kVA.
Aluminum enamelled wire winding is suitable for the industrial production of enamelled aluminum wire immersed in transformer oil. It is the most important contribution in the manufacturing industry of distribution oil immersed transformer in the recent period.
The main advantages of using painted wire in high voltage winding are:
Reduce insulation volume;
Improve the heat dissipation of winding;
Improve the distribution of impulse voltage, so as to improve the impact strength of winding.
Using aluminum enamelled wire can greatly improve the parameters of oil immersed transformer for power distribution. The transformer with this winding not only has light weight and low loss, but also has high overvoltage resistance, so its service life is longer.
The reason why aluminum enamelled wire can not be quickly used in oil immersed transformer is that it is unable to find transformer oil that can resist heat for a long time and paint suitable for insulation that can resist the aging of insulation system. It also puts forward a series of strict requirements for insulating paint, which requires high wear resistance, good elasticity and high solvent corrosion resistance. Polyvinyl formal paint can meet these strict requirements.
The use of aluminum enamelled wire usually does not require special adjustment of the winding process, and there is no need to make major changes in the process equipment. The structure of the winding made of enameled wire is usually no different from that of the original winding, so it can be used as either a single winding composed of multi-layer coils or a dense multi-layer winding. Use cable paper insulation intermediate layer to separate each layer. Some transformer manufacturers also began to use high-voltage windings made of thin aluminum strip, which are separated by insulating film when winding. However, for quite a long time in the future, the manufacturers of distribution transformers with aluminum painted wire multi-layer winding still account for the majority, mainly because it does not need to be changed in the process equipment.
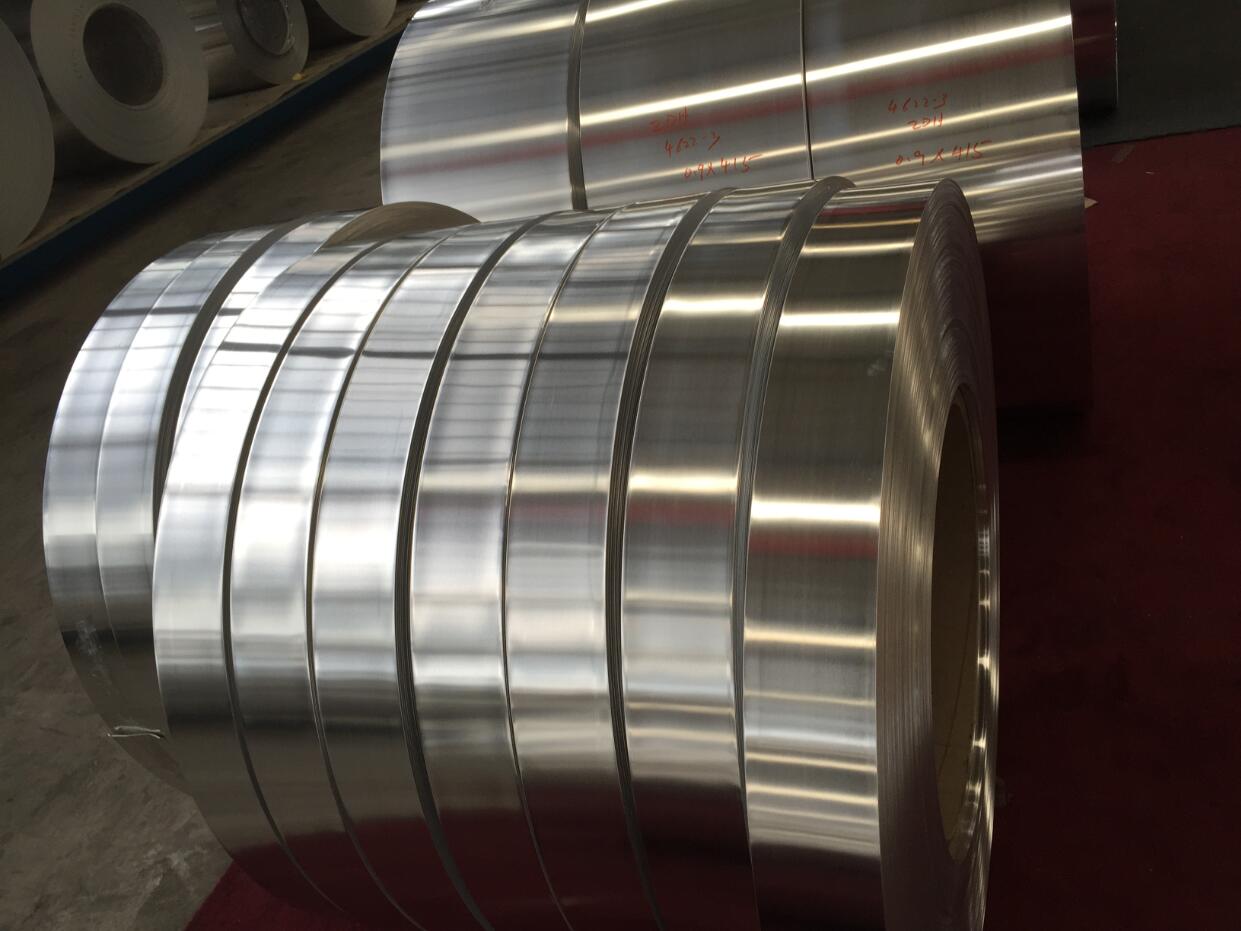
Winding made of thin aluminum strip and aluminum foil
At present, windings made of thin aluminum strip are being used in oil immersed transformers and air-cooled transformers. Although the initial research focused on the use of aluminum strip and aluminum foil in high-voltage winding, the application in low-voltage winding has greater significance. The thin aluminum strip low-voltage winding is either single or composed of two plate coils connected in parallel. The winding itself consists of a smooth aluminum strip and an intermediate insulating layer, which protrudes 10 to 15 mm on both sides of the aluminum strip. The space at both ends is filled with boundary insulating material.
In the oil immersed transformer, this insulating layer is composed of adhesive tape, which is actually the continuation of aluminum tape in the axial direction. In air-cooled transformers, the space at both ends of the winding is usually filled with curable asphalt.
The beginning and end of the winding are tapped with aluminum strip, which is welded to the boundary line turn.
Compared with the original winding, the production process of thin aluminum strip winding is relatively simple. In particular, these windings are plate-shaped, which is simpler without axial lifting and climbing. When winding, aluminum tape, intermediate insulation layer and balanced insulation are wound at the same time, because the winding machine can be wound at the highest speed after adjustment, so as to greatly improve the winding efficiency.
From the point of view of reducing the variety of materials required for the winding, it is also appropriate to adopt the low-voltage winding made of thin aluminum strip, because this kind of winding does not need the compensation balancer and pressure ring supporting the insulator. When winding multiple parallel coils, it is not necessary to wind each conductor alternately.
However, special process equipment is required for winding thin aluminum strip low-voltage winding. In addition to reliably winding aluminum strip, intermediate insulation layer and balance insulation layer, this device must also be able to weld taps.
The modern winding machine for winding thin aluminum strip windings produced in the recent period can wind two aluminum strips at the same time. This kind of winding machine uses tungsten inert gas shielded welding to weld taps and helium as shielding gas. This welding method can not only weld the tap, but also weld the aluminum strip, which can make the most effective use of winding materials and improve the labor productivity.
Some distribution transformer manufacturers attempt to use self-adhesive intermediate insulation layer or heating curing insulation layer. With the help of such insulation, the winding can have high mechanical strength and short-circuit current resistance.
In recent years, the biggest change in the production of distribution transformer coil is the use of aluminum enameled wire, and the transition to winding with thin aluminum belt. The cooling system of oil immersed distribution transformer has also been improved. The air tightness of oil tank is a development trend, and there are also significant changes in the production process of transformer core.
It can be said that the historic changes in the distribution transformer dance represented by the production of enamelled aluminum wire, antioxidant transformer oil and cast insulated transformer are as significant as the use of directional silicon steel strip during the postwar period.
At present, the high-voltage winding of distribution oil immersed transformer is characterized by the use of enameled aluminum wire and aluminum strip. When the cross-section of the wire is not large, the paint can not be used only when the cross-section of the wire is not large. Fundamental changes have also taken place in the low-voltage winding. At present, the unified winding made of thin aluminum strip and interlayer insulation winding is gradually replacing various types and models of windings for transformers with a capacity of 100 to 1600 kVA.
Aluminum enamelled wire winding is suitable for the industrial production of enamelled aluminum wire immersed in transformer oil. It is the most important contribution in the manufacturing industry of distribution oil immersed transformer in the recent period.
The main advantages of using painted wire in high voltage winding are:
Reduce insulation volume;
Improve the heat dissipation of winding;
Improve the distribution of impulse voltage, so as to improve the impact strength of winding.
Using aluminum enamelled wire can greatly improve the parameters of oil immersed transformer for power distribution. The transformer with this winding not only has light weight and low loss, but also has high overvoltage resistance, so its service life is longer.
The reason why aluminum enamelled wire can not be quickly used in oil immersed transformer is that it is unable to find transformer oil that can resist heat for a long time and paint suitable for insulation that can resist the aging of insulation system. It also puts forward a series of strict requirements for insulating paint, which requires high wear resistance, good elasticity and high solvent corrosion resistance. Polyvinyl formal paint can meet these strict requirements.
The use of aluminum enamelled wire usually does not require special adjustment of the winding process, and there is no need to make major changes in the process equipment. The structure of the winding made of enameled wire is usually no different from that of the original winding, so it can be used as either a single winding composed of multi-layer coils or a dense multi-layer winding. Use cable paper insulation intermediate layer to separate each layer. Some transformer manufacturers also began to use high-voltage windings made of thin aluminum strip, which are separated by insulating film when winding. However, for quite a long time in the future, the manufacturers of distribution transformers with aluminum painted wire multi-layer winding still account for the majority, mainly because it does not need to be changed in the process equipment.
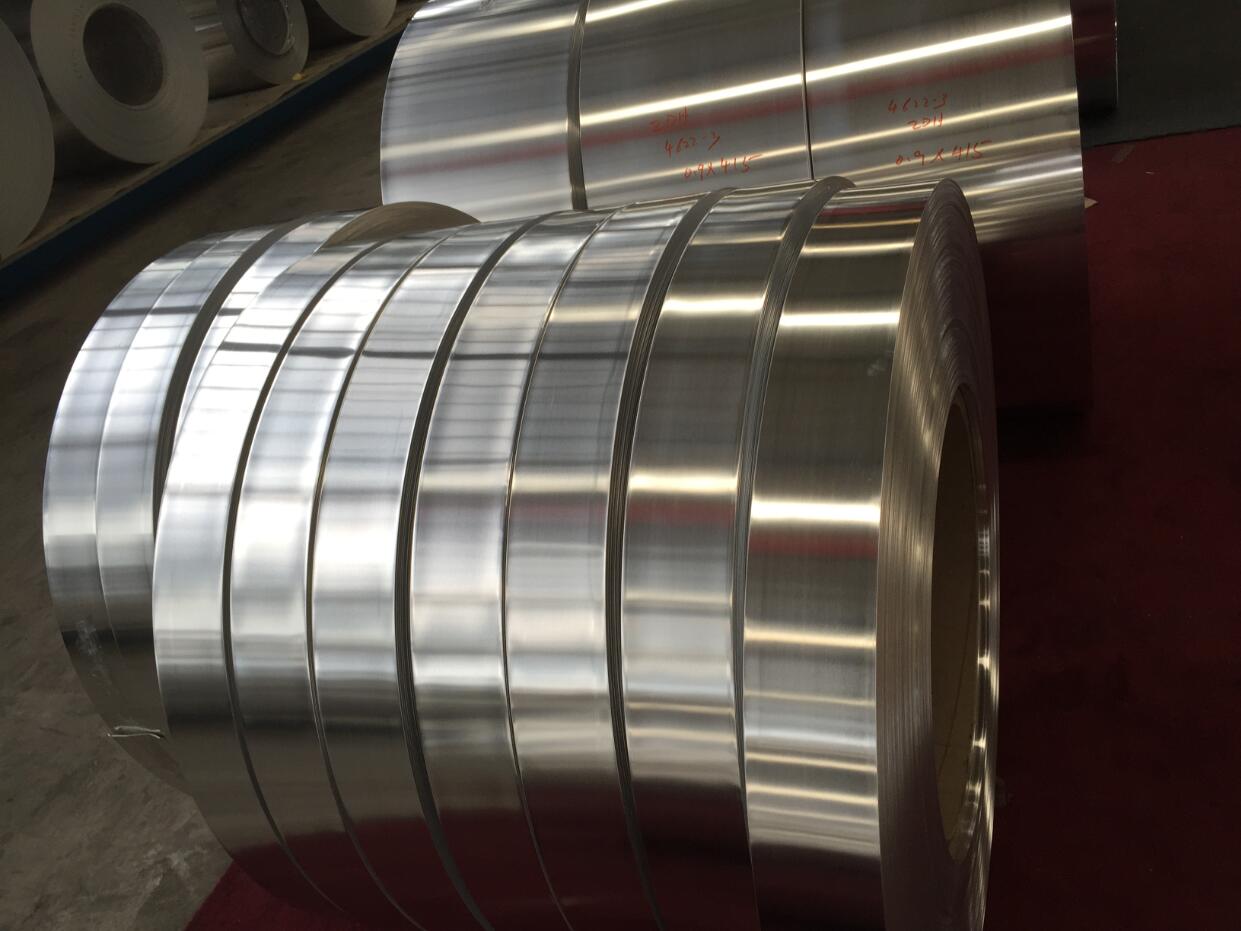
Winding made of thin aluminum strip and aluminum foil
At present, windings made of thin aluminum strip are being used in oil immersed transformers and air-cooled transformers. Although the initial research focused on the use of aluminum strip and aluminum foil in high-voltage winding, the application in low-voltage winding has greater significance. The thin aluminum strip low-voltage winding is either single or composed of two plate coils connected in parallel. The winding itself consists of a smooth aluminum strip and an intermediate insulating layer, which protrudes 10 to 15 mm on both sides of the aluminum strip. The space at both ends is filled with boundary insulating material.
In the oil immersed transformer, this insulating layer is composed of adhesive tape, which is actually the continuation of aluminum tape in the axial direction. In air-cooled transformers, the space at both ends of the winding is usually filled with curable asphalt.
The beginning and end of the winding are tapped with aluminum strip, which is welded to the boundary line turn.
Compared with the original winding, the production process of thin aluminum strip winding is relatively simple. In particular, these windings are plate-shaped, which is simpler without axial lifting and climbing. When winding, aluminum tape, intermediate insulation layer and balanced insulation are wound at the same time, because the winding machine can be wound at the highest speed after adjustment, so as to greatly improve the winding efficiency.
From the point of view of reducing the variety of materials required for the winding, it is also appropriate to adopt the low-voltage winding made of thin aluminum strip, because this kind of winding does not need the compensation balancer and pressure ring supporting the insulator. When winding multiple parallel coils, it is not necessary to wind each conductor alternately.
However, special process equipment is required for winding thin aluminum strip low-voltage winding. In addition to reliably winding aluminum strip, intermediate insulation layer and balance insulation layer, this device must also be able to weld taps.
The modern winding machine for winding thin aluminum strip windings produced in the recent period can wind two aluminum strips at the same time. This kind of winding machine uses tungsten inert gas shielded welding to weld taps and helium as shielding gas. This welding method can not only weld the tap, but also weld the aluminum strip, which can make the most effective use of winding materials and improve the labor productivity.
Some distribution transformer manufacturers attempt to use self-adhesive intermediate insulation layer or heating curing insulation layer. With the help of such insulation, the winding can have high mechanical strength and short-circuit current resistance.
RELATED READ:
- Foil for electrolytic capacitors2015.3.19
- Copper-Clad Aluminum Wire (CCA)2015.3.19
- 5052 aluminum strip for shutters2015.3.19
- Application of aluminum semi-finished products in e2015.3.19
- Copper clad aluminum enamelled round wire2015.3.19